Leichtlaufzylinder und dichtungslose Zylinder kommen generell seltener in der Pneumatik vor, sind jedoch in einigen Bereichen der Technik unverzichtbar.
Wo sind aber die großen Unterschiede zu den standardisierten Pneumatik Zylindern am Markt?
Ein Leichtlaufzylinder unterscheidet sich von einem Standardzylinder vor allem dadurch, dass die Losbrechkraft zum Betätigen des Zylinders deutlich kleiner ist. Während ein Standardzylinder ca. 300-600mbar Druck benötigt um die Losbrechkraft zu überwinden, sind dies bei Leichtlaufzylindern nur ca. 10-100mbar.
Durch verschiedene Eigenschaftsänderungen wird hier versucht den sog. „Stick-Slip“ Effekt so gering wie möglich zu halten. Der Stick-Slip-Effekt tritt immer dann auf, wenn die Haftreibung deutlich größer als die Gleitreibung ist. Durch die Dichtungen an Kolbenstange und Kolben tritt am Pneumatik Zylinder eine vergleichsweise stark ausgeprägte Haft- und Gleitreibung auf.
Wie kann man diese Reibung minimieren?
- Optimierung der Materialeigenschaften
- Für Leichtlaufsysteme können spezielle Elastomere mit reibungsoptimierten Formen und Materialien eingesetzt werden. Je geringer die Fläche ist, an der das Elastomer an der Fläche aufliegt umso geringer ist auch die Haftreibung.
- Auch die Härte der Dichtungen hat einen wesentlichen Einfluss auf die Reibung.
- Beschichtungen der Gleitpartner
- Beschichtungen können die Gleiteigenschaften sowohl von den Dichtungen als auch von den metallischen Gegenflächen stark vermindern. Gängige Beschichtungen sind meist auf PTFE Basis oder ähnlichen Gleitbeschichtungen.
- Anpassung der Vorspannung der Dichtungen
- Eine Verminderung der Vorspannung der Dichtung führt ebenfalls zu deutlichen Reduktionen der Reibung. Hierbei wird die Anpresskraft der Kolbendichtung auf das Zylinderrohr so lange vermindert bis gerade noch sicher abgedichtet wird. Erreicht wird dies indem man die Auflagefläche der Kolbendichtung am Kolben auf ein gewünschtes Maß reduziert.
- Gleiche Vorgangsweise gilt auch für die Stangendichtung.
Ein dichtungsloser Zylinder geht bei der Reduktion der Reibung noch einen deutlichen Schritt weiter. Wie der Name schon verrät verzichtet der dichtungslose Zylinder bei der Abdichtung völlig auf jegliche Elastomer Dichtungen. Damit liegt aber auch die Hauptproblematik dieser Systeme auf der Hand. Eine Abdichtung zwischen Kolben und Zylinderrohr erfolgt ausschließlich über einen perfekt ausgeführten minimalen Luftspalt im Bereich von < 0,01mm.
Je größer der Luftspalt ist umso „undichter“ ist ein dichtungsloser Zylinder.
Da er jedoch keine Elastomer Dichtung trägt, ist der dichtungslose Zylinder nahezu reibungsfrei und fährt bereits bei wenigen mbar Druck aus. In unserem Beispiel fährt der dichtungslose Zylinder bereits bei 2-3mbar aus. Damit braucht ein Standardzylinder ungefähr 200mal mehr Druck als ein dichtungsloser Zylinder zum Ausfahren.
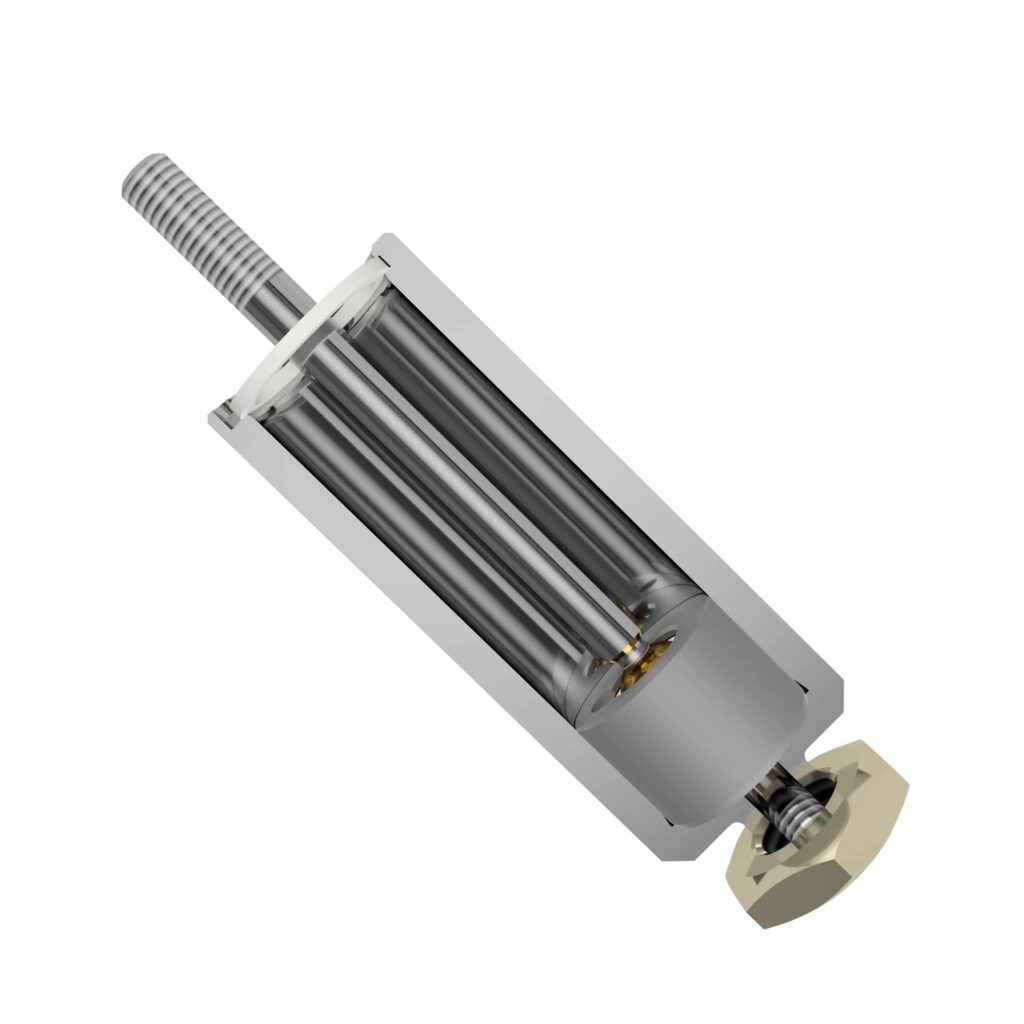